It is already too late. I have observed that work on swimming pools is all done in late spring, when it is already too late for the coverings to mature properly. This is the main cause of headaches for those who face the problem of coating their pools, whatever the material they chose. The tank environment differs from a normal waterproofing/coating job in at least two fundamental variables: the water is aggressive (chlorine, salt or oxygen) and above all it exerts a fair amount of hydrostatic pressure. Many materials are able to resist perfectly once they have matured properly, but premature filling of the pool may lead to detachment, swelling and discolouration of the coating.
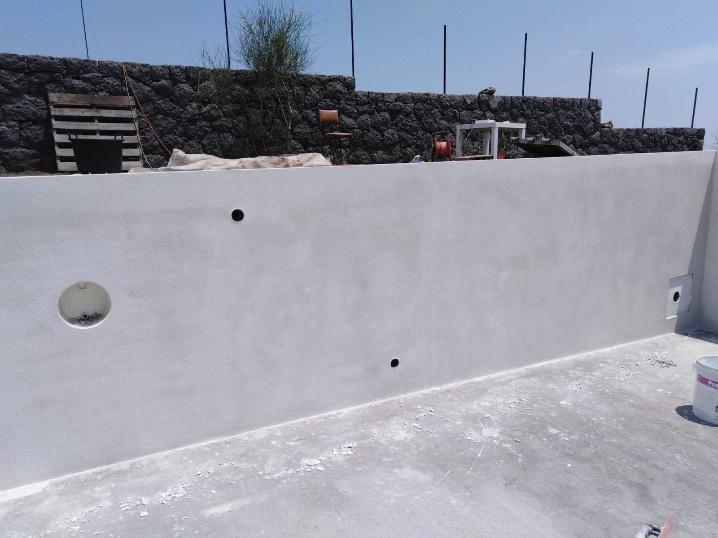
If you want to proceed with a cement material, remember that curing time is at least 4 weeks after completion of the work. Any transparent protective coatings that may be applied on top do not change this parameter, as it is not possible to think that a few microns of coating can stop water under pressure.
The other key aspect to be considered is waterproofing against the ground, i.e. on the side opposite to that affected by the filling: in the case of in-ground pools or tubs, the water that runs from the ground to the inside must also be considered. It is much easier for a coating to come off because of this mechanism, especially during periods when the pool is temporarily empty for cleaning and maintenance.Based on the assumption of a suitably sized swimming pool made of reinforced concrete, I will illustrate below the recipe using Ecobeton products for coating the pool:
1) Concrete waterproofing with Evercrete® Vetrofluid. This involves waterproofing the concrete against rainwater infiltration from the surrounding soil. Vetrofluid is an impregnating agent which, when sprayed onto the surface, migrates spontaneously into the concrete casting, forming a silicate matrix which permanently saturates the porosity of the concrete. It can be applied either from the outer side (preferable) or from the opposite side, because thanks to its penetration, it also resists negative thrust (yield: 400-500 g/m2).
2) Make the surface sufficiently rough. Formwork casting almost always leaves the concrete surface too smooth for adequate adhesion of subsequent layers. A bush hammer or a simple orbital sander can easily solve the problem.
3) Restore any discontinuities in the casting such as gravel nests and ensure that there are no exposed through bodies such as formwork blades.
4) Coating with the new micro-cement suitable for coating swimming pools, Poseidone. Poseidone performs a dual function as it both evens the surface of the casting and provides an aesthetic finish. Poseidone should be applied in several coats, incorporating an alkali-resistant glass fibre mesh to ensure a uniform coating thickness. (Yield: 6-8 kg/m2).
5) Possible protection with GiGi Sealer to facilitate cleaning of the tank and to preserve any chosen pigment. The protective finish cannot be deemed a waterproofing agent.
6) Wait 4 weeks before filling.
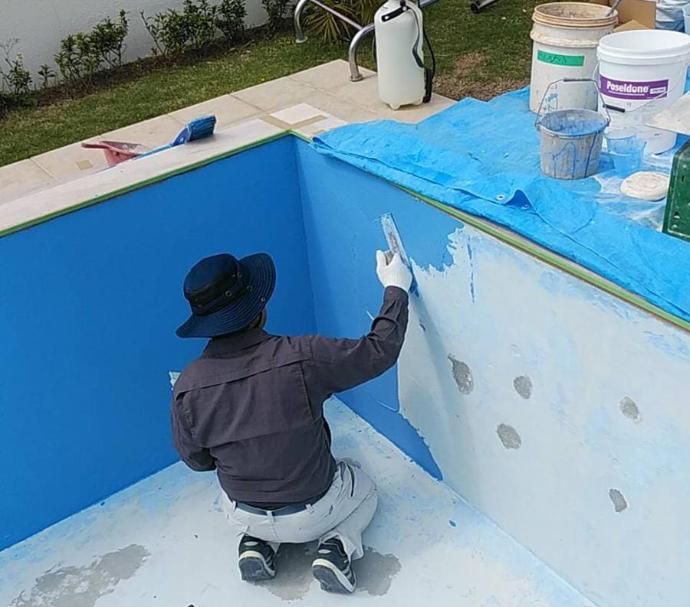
Coating of a swimming pool with deep blue dyed Poseidone.
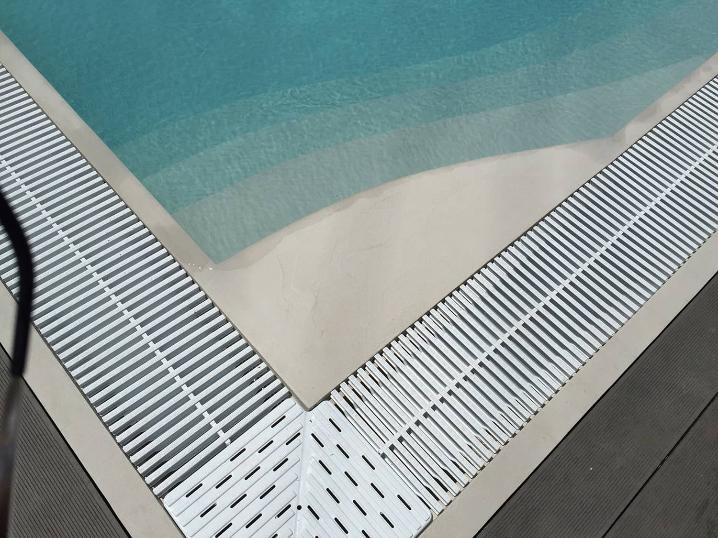
A note on colour:
Swimming pools and microcement.